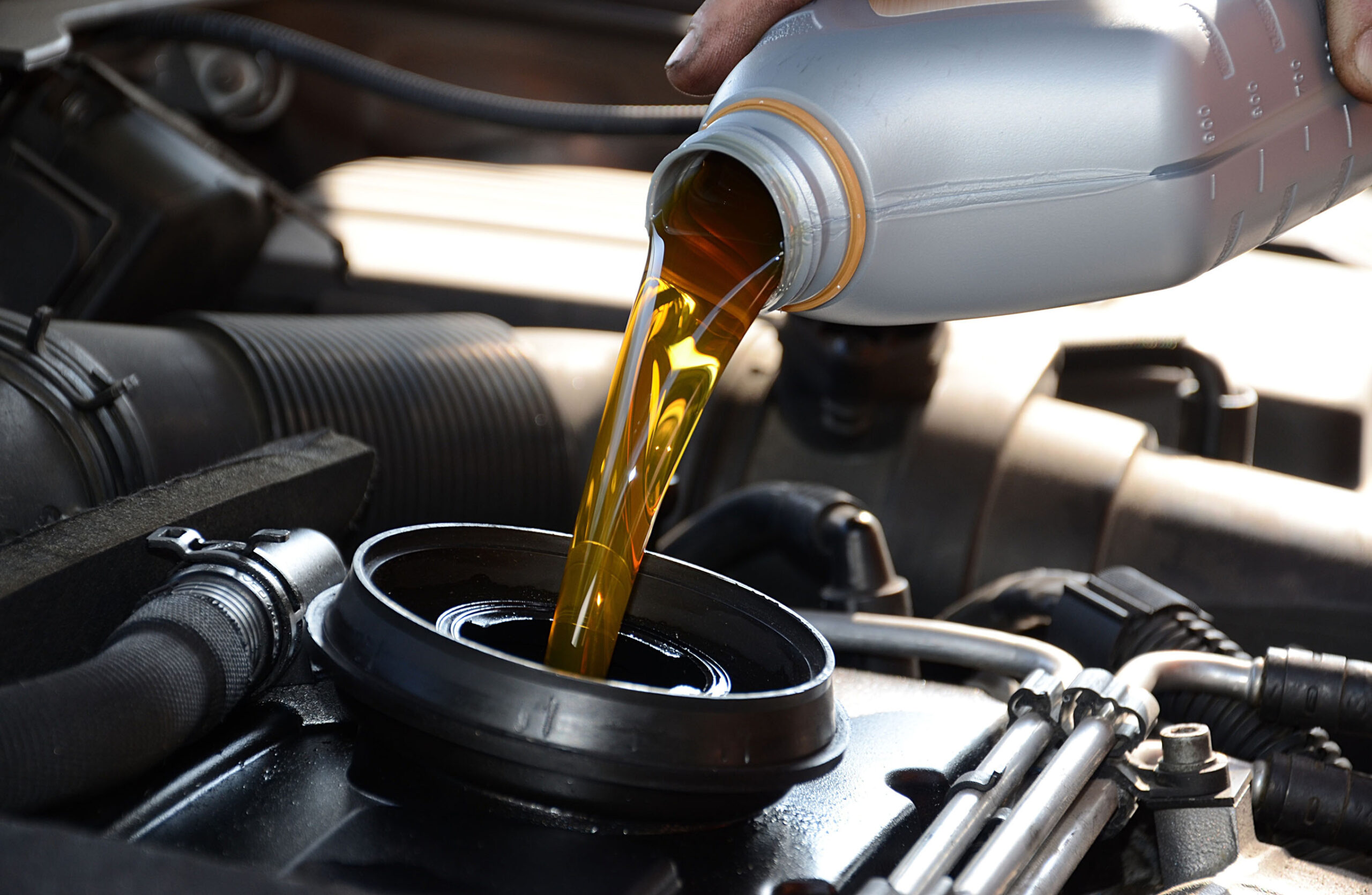
Top 8 Advantages of Synthetic Oil and Lubricants
Today, businesses have to find various methods to boost the efficiency of their operations. Lubricants and synthetic oil are widely used in different types of industries. They help to keep your engine working smoothly for years.
Synthetic oils and lubricants are used in many car companies and other industries. Let us further discuss the benefits of synthetic oil and lubricants for industries.
Major benefits of synthetic oil and lubricants
Synthetic oil is very effective and used in various applications. It includes a unique molecular structure and provides many benefits such as:
1. Contains a low amount of impurities
Synthetic oil is effective in removing impurities from the crude oil. On the other hand, ordinary oil contains impurities such as phosphorus, sulfur, oxygen, and nitrogen. Synthetic oil can also be broken into a molecular structure and increases efficiency in the engine.
2. High viscosity index
nother benefit of synthetic oil is that it has a higher viscosity index than other components. It can be used in any kind of weather or temperature in the industry. Synthetic oil maintains a high flow ability rate even at a low temperature.
3. Uniform composition
Unlike conventional oil, the synthetic oil is made of base oils extracted from the ground. It is refined and broken down into a uniform molecular structure. Synthetic oil gives better lubrication than conventional oils because of high stability.
4. Contains high flash point
While normal mineral oils have a low flash point of 440 degrees F, synthetic oil has a higher flash point. It is less flammable and a safer solution than other mineral oils. Moreover, synthetic oil is perfect for advanced engine technology as it faces a higher temperature.
5. Gives good engine efficiency
Another benefit of using synthetic oil is that it makes engines more efficient. Engines containing synthetic oil need less horsepower and force to carry heavy loads. They will gain better efficiency with the regular use of synthetic oil.
6. Biodegradable product
Synthetic oil is a biodegradable product and helps to remove engine waste easily. It is also easier to break down synthetic oil into a uniform structure of molecules. Synthetic oil is not dangerous even if it is split.
7. Long service life
Synthetic oil and lubricants have longer service life than conventional oils. They do not need any frequent oil changes. Certain typical change intervals are between 5000 and 7000 miles. Some synthetic oils have longer intervals than other products.
8. Long shelf life
Synthetic oils and lubricants have a longer shelf life than other conventional oils. They also work for a longer time than other conventional oils. Synthetic oils decrease lubricant expenses with time.
Conclusion
These are the major benefits of synthetic oils and lubricants. They are safe to use in different types of engines. You can get premium quality synthetic oils and lubricants at an affordable range from Tribolubes. We are the Best Engine Oil Manufacturer In India with a huge customer base.
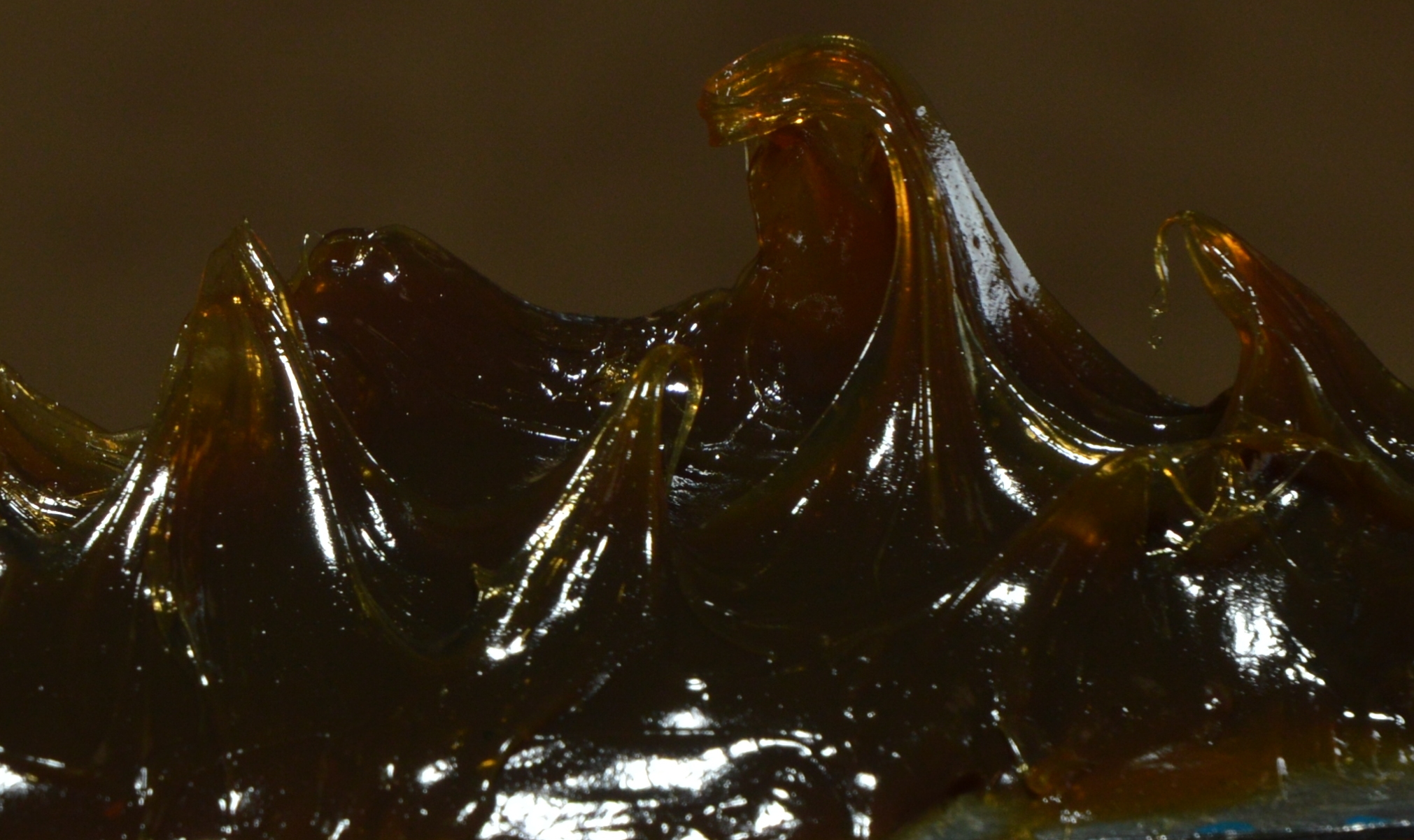
What Is the Difference Between Regular Grease and Lithium Grease?
Grease is an important component used in various kinds of industries. It is widely used in different applications such as garden gates, half-tracks, hinges, and mechanical devices. Grease comes in different types for various industrial uses and applications.
Regular grease and lithium grease are the most common kinds of greases used in different industries. In this blog, we will talk about regular grease and lithium grease and the differences between them.
Meaning of regular grease and lithium grease
Before knowing the differences between regular grease and lithium grease, let us know the meaning of both these terms. Regular grease is a kind of clay-based grease that can withstand high pressure and high heat. It is used in various types of industries.
Lithium grease is mostly used in domestic settings. It is different from regular grease and cannot withstand high pressure or heat. This grease is widely used in making hinges loose or removing dust. Besides, lithium grease also helps to develop some hair products.
Key differences between regular grease and lithium grease
Both regular grease and lithium grease are different from each other in many ways such as:
1. Heat resistance
Regular grease can resist high pressure as well as heat. It is used in many applications in several industries and companies. On the other hand, the lithium grease cannot handle the high pressure and heat. This kind of grease is used in many industries such as metal, plastic, metallic, and mechanical equipment.
2. Form
Lithium grease is thicker than regular grease. It is available in the form of aerosol and used in several metal applications as a heavy-duty lubricant. Lithium greases release a small portion of oil while used in different industries. It is lubricated with a protective layer. You can use lithium gas in different applications.
Regular grease is available in the form of clay and can hold high pressure and temperature as well. It is free of additives and chemicals and used in many applications.
3. Benefits
Lithium grease has more benefits than regular grease in various industries. It also provides better than regular grease. On the other hand, the regular grease gives lubrication for a short time.
Lithium grease does not drip or flow during use or application in the industries. It can be used in several load-bearing connections and reduces wear and friction. Unlike regular grease, you can use lithium grease in many outdoor applications.
4. Uses
Lithium grease is used for lubricating metals and running various components. On the other hand, regular grease is used in industries like hair products, skincare, and so on.
Lithium grease is mostly used in domestic settings. Regular grease is used to decrease friction in the machines and other components.
Conclusion
Regular and lithium grease have their benefits in various industries. They are widely used in the different applications of various industries. Grease is useful in lubricating various components and parts of the machinery and helps them work smoothly. If you are also looking for a Grease Manufacturer in India, you can get in touch with Tribo Lubes. We have been in this market for many years and have a lot of experience in manufacturing the best products.
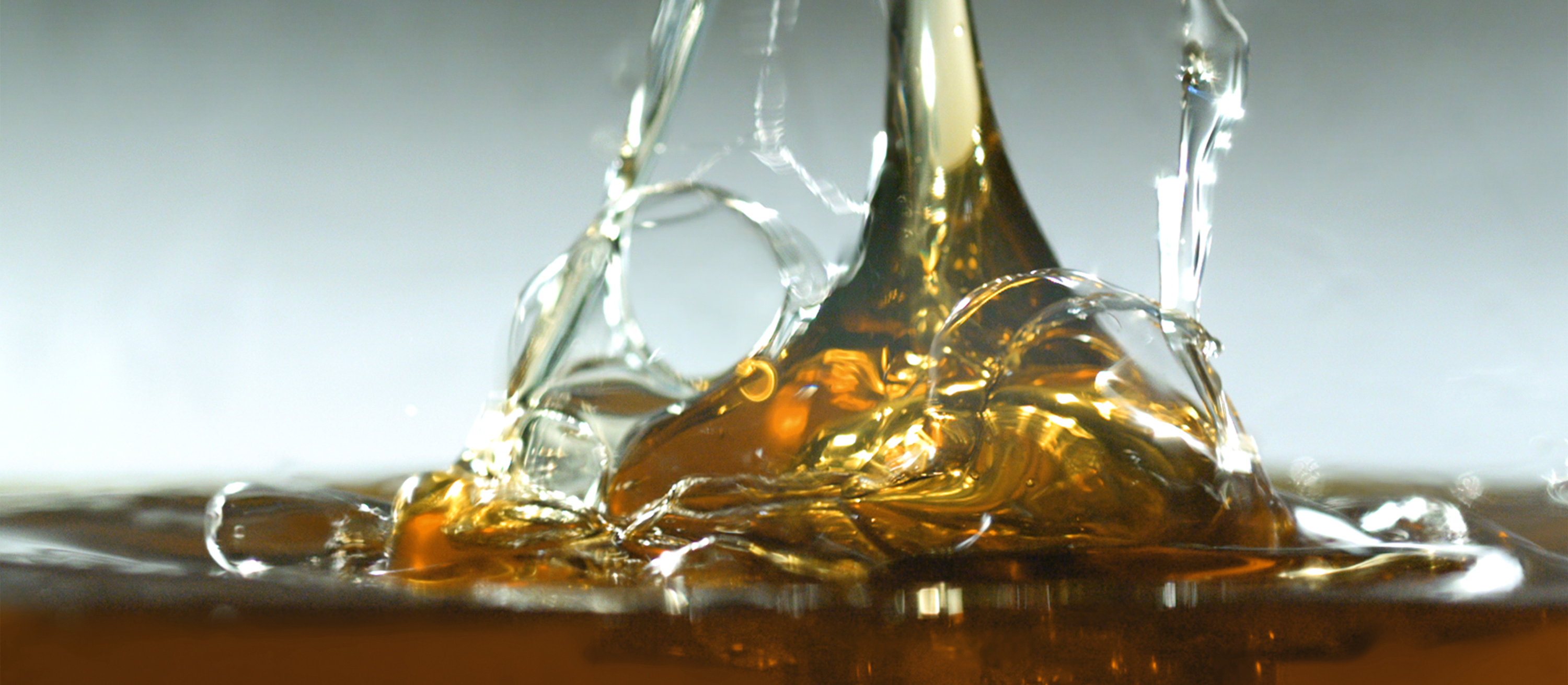
The Importance of Proper Grease
Proper grease application is crucial across various industries and applications, ranging from automotive to manufacturing and beyond. Here are several key reasons why proper grease is important:
1. Friction Reduction:
- Grease is primarily used as a lubricant to reduce friction between moving parts. By properly applying grease, you ensure that the friction between components is minimized, which in turn reduces wear and tear, prolonging the lifespan of the equipment.
2. Wear Protection:
- Grease forms a protective layer between metal surfaces, preventing direct contact and reducing wear. Properly applied grease acts as a barrier against contaminants such as dirt, dust, and moisture, which can accelerate wear and lead to premature equipment failure.
3. Corrosion Prevention:
- Grease helps to inhibit corrosion by sealing out moisture and oxygen, which are primary catalysts for rust formation. By creating a protective barrier, grease safeguards metal surfaces from environmental elements, extending the life of machinery and equipment.
4. Temperature Stability:
- Grease can withstand high temperatures without losing its lubricating properties. Properly selected grease with the appropriate temperature range ensures that machinery operates smoothly even under extreme conditions, preventing overheating and component failure.
5. Sealing Properties:
- Grease can act as a sealant, preventing leaks and contamination. Proper application of grease helps maintain the integrity of seals and gaskets, ensuring that equipment operates efficiently and minimizing the risk of fluid loss or ingress of contaminants.
6. Noise Reduction:
- In addition to lubricating moving parts, grease can also help dampen vibrations and reduce noise levels generated by machinery. Properly lubricated components operate more quietly, creating a safer and more comfortable working environment.
7. Efficiency and Performance:
- Properly lubricated equipment operates more efficiently, requiring less energy and reducing operational costs. By ensuring that machinery is adequately lubricated with the right grease, you optimize performance and productivity while minimizing downtime for maintenance and repairs.
8. Safety:
- Proper grease application is essential for maintaining safe working conditions. Inadequate lubrication can lead to equipment malfunctions, breakdowns, and accidents. By following proper grease application procedures, you help mitigate risks and ensure the safety of personnel and assets.
In summary, the importance of proper grease application cannot be overstated. From reducing friction to choosing the right Grease Manufacturer In India & preventing corrosion and enhancing safety, the right grease, applied correctly, is essential for maintaining the performance, reliability, and longevity of machinery and equipment across various industries.
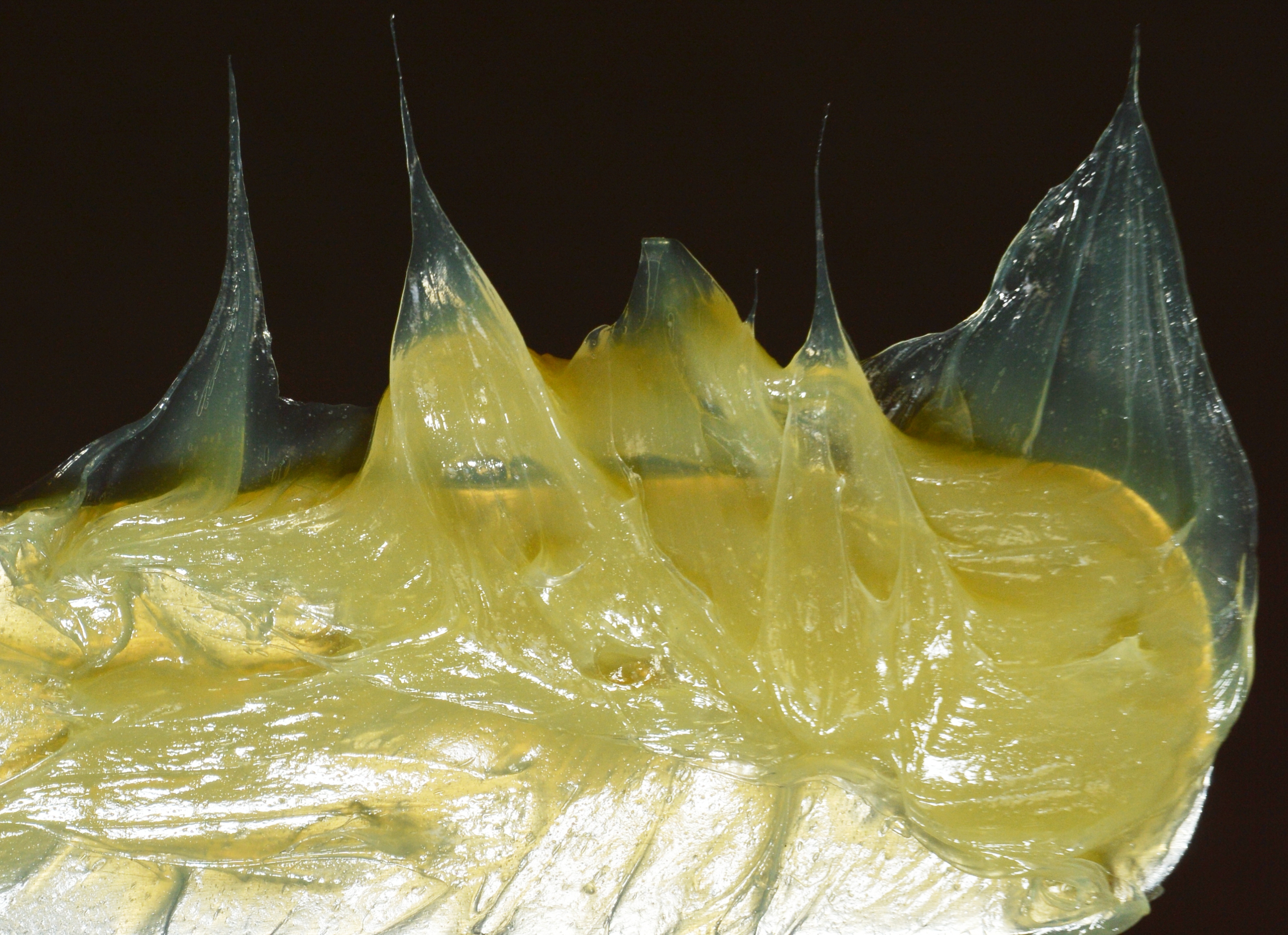
The Importance of Proper Grease and Lubrication
Proper grease and lubrication play a crucial role in the functioning and longevity of machinery and mechanical systems across various industries. Here are some key reasons why they are important:
1. Reduced Friction:
- Grease and lubricants reduce friction between moving parts in machinery, which helps to minimize wear and tear. This friction reduction is essential for preventing overheating and premature failure of components.
2. Extended Component Life:
- By reducing friction, proper lubrication helps to extend the life of components such as bearings, gears, and shafts. This not only saves on replacement costs but also reduces downtime for maintenance and repairs.
3. Improved Efficiency:
- Well-lubricated machinery operates more efficiently. Reduced friction means less energy is wasted in overcoming resistance, leading to lower energy consumption and increased productivity.
4. Prevention of Corrosion and Rust:
- Grease and lubricants create a protective barrier that helps to prevent corrosion and rust on metal surfaces. This is particularly important in environments with high humidity, exposure to water, or acidic conditions.
5. Noise Reduction:
- Proper lubrication can also help to reduce noise generated by moving parts. This is especially beneficial in environments where noise pollution is a concern, such as factories or residential areas near industrial facilities.
6. Temperature Regulation:
- Lubricants help to dissipate heat generated by friction, contributing to temperature regulation within machinery. This is critical for preventing overheating, which can lead to component failure and safety hazards.
7. Sealing and Contamination Control:
- Grease and lubricants can act as seals, helping to prevent the entry of contaminants such as dust, dirt, and moisture into sensitive components. This is essential for maintaining the cleanliness and reliability of machinery, especially in harsh operating environments.
8. Compliance with Regulations:
- In many industries, proper lubrication is not just a matter of efficiency and performance but also a legal requirement. Failure to adhere to lubrication standards and maintenance schedules can result in fines, penalties, and liability issues.
Overall, proper grease and lubrication are essential for maintaining the performance, reliability, and safety of machinery and mechanical systems. Investing in Best Quality Grease Manufacturer. Grease & Lubrication implementing is a regular maintenance schedule can yield significant cost savings and operational benefits over the long term.
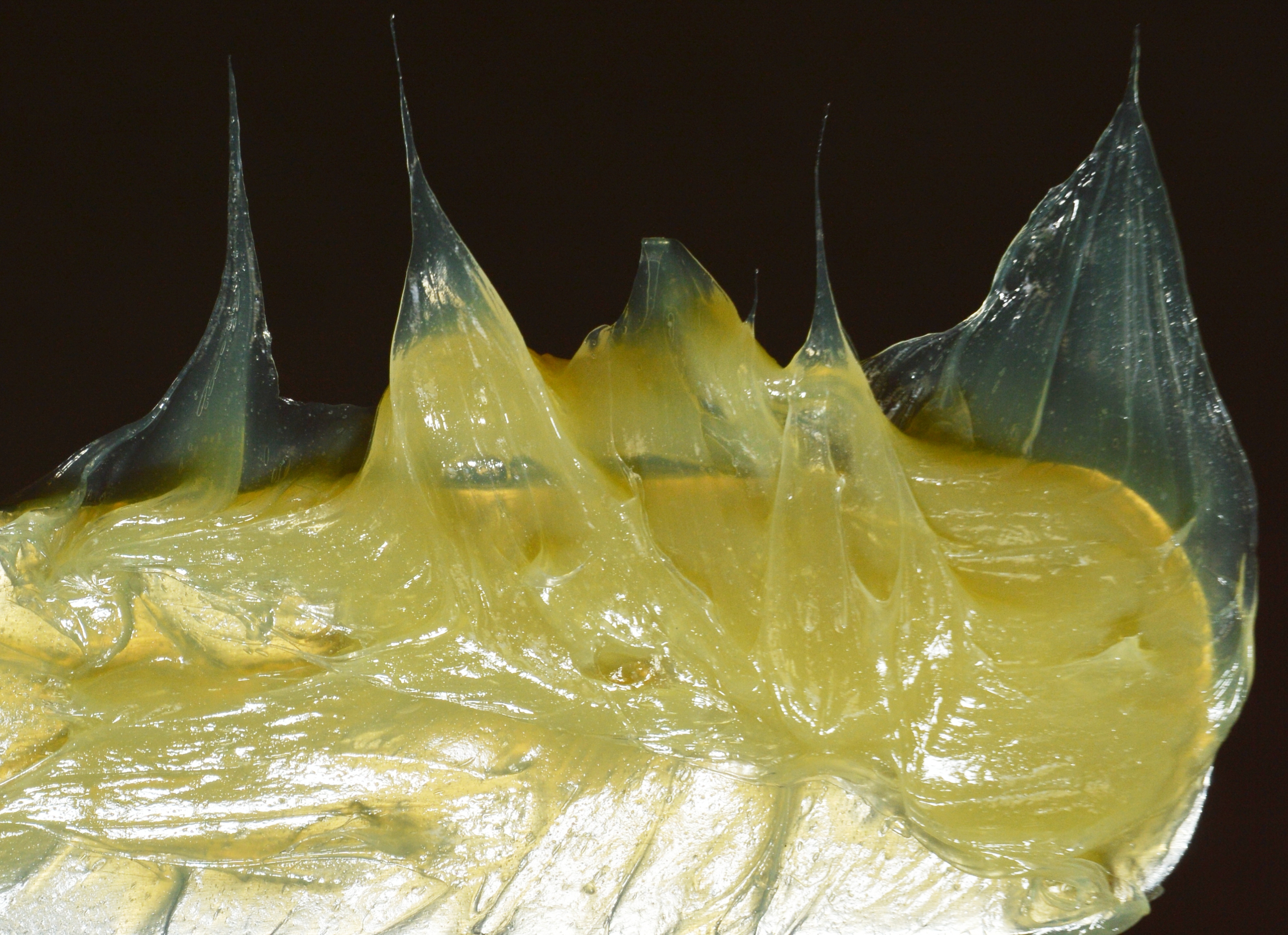
How to Find the Best Greace Manufacturer in India
Finding the best grease manufacturer in India involves a systematic approach to evaluating various factors. Here’s a step-by-step guide to help you identify and select a reliable grease manufacturer:
1. Define Your Requirements:
Clearly define your specific requirements for grease, such as the type (lithium, calcium, etc.), application (automotive, industrial, marine), and performance specifications.
2. Research and List Potential Manufacturers:
Conduct online research and compile a list of potential grease manufacturers in India. Look for companies with a solid reputation and experience in producing the type of grease you need.
3. Check Industry Certifications:
Ensure that the manufacturer holds relevant certifications and complies with industry standards. Look for certifications such as ISO 9001:2015 for quality management systems and other specific certifications related to grease manufacturing.
4. Evaluate Experience and Reputation:
Consider the manufacturer’s experience in the industry. Look for customer reviews, testimonials, and case studies to gauge their reputation. A manufacturer with a good track record is likely to provide quality products.
5. Assess Production Facilities:
Evaluate the manufacturer’s production facilities. Modern and well-maintained facilities are indicative of a commitment to quality. Check if they have the necessary equipment and technology for producing grease to meet your specifications.
6. Review Product Range and Innovation:
Check the manufacturer’s product range and whether they invest in research and development. A manufacturer that stays abreast of industry trends and continuously innovates is more likely to provide high-quality products.
7. Quality Control Measures:
Inquire about the manufacturer’s quality control measures. Ask about their testing processes, quality assurance practices, and adherence to international standards. A reliable manufacturer will have stringent quality control procedures in place.
8. Supply Chain and Distribution Network:
Assess the manufacturer’s supply chain capabilities and distribution network. A well-established supply chain ensures timely delivery of products, minimizing disruptions in your operations.
9. Cost and Pricing Structure:
Obtain detailed quotes from potential manufacturers. While cost is an important factor, it should not be the sole determinant. Consider the overall value, including product quality, reliability, and customer service, when evaluating pricing structures.
10. Customer Support and Service:
Evaluate the manufacturer’s customer support and service. Responsive and reliable customer service can be crucial in addressing any issues or concerns that may arise during the procurement process.
11. Visit the Manufacturer if Possible:
If feasible, consider visiting the manufacturing facilities. This firsthand experience can provide insights into the manufacturer’s capabilities, production processes, and overall commitment to quality.
12. Negotiate Terms and Conditions:
Once you’ve narrowed down your options, negotiate terms and conditions, including payment terms, delivery schedules, and any specific requirements you may have.
By following these steps, you can make an informed decision when selecting a grease manufacturer in India. Always prioritize quality, reliability, and compatibility with your specific needs.
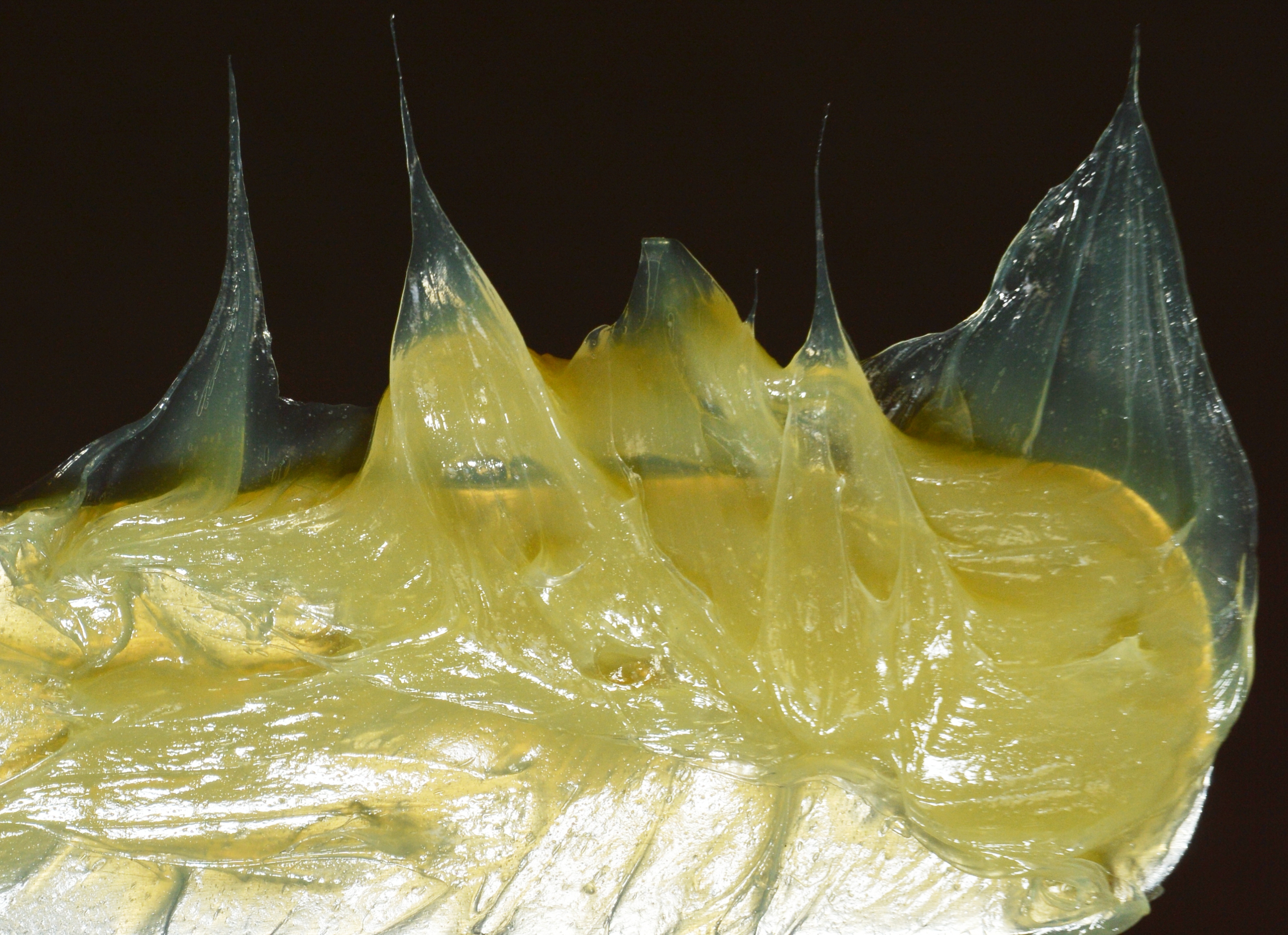
The Major Role of Grease Manufacturer in the Lubrication Industry
Grease manufacturers play a crucial role in the lubrication industry by producing and supplying a variety of greases that are essential for the proper functioning of machinery and equipment. Grease is a semisolid lubricant composed of a base oil, thickener, and additives. It is used to reduce friction, prevent wear, and provide protection against corrosion in a wide range of applications, from automotive and industrial machinery to household appliances. The major roles of grease manufacturers in the lubrication industry include:
1. Formulation and Production:
Grease manufacturers formulate greases by carefully selecting base oils, thickeners, and additives to create a product with specific properties suitable for various applications. The manufacturing process involves blending these components in precise proportions to achieve the desired consistency and performance characteristics.
2. Product Innovation:
As technology advances and industry requirements evolve, grease manufacturers play a key role in developing new formulations and improving existing products. They may invest in research and development to create greases with enhanced properties such as extreme pressure resistance, high-temperature stability, water resistance, and compatibility with different materials.
3. Quality Control:
Grease manufacturers are responsible for maintaining strict quality control standards throughout the production process. This includes testing raw materials, monitoring the manufacturing process, and conducting thorough quality checks on the final product to ensure that it meets industry specifications and performance requirements.
4. Customized Solutions:
Grease manufacturers often work closely with customers to understand their specific lubrication needs and challenges. They may offer customized grease formulations tailored to meet the unique requirements of particular applications, industries, or operating conditions.
5. Supply Chain Management:
Grease manufacturers are involved in managing the supply chain to ensure a steady and reliable distribution of their products. This involves coordinating the sourcing of raw materials, production scheduling, packaging, and timely delivery to distributors, retailers, and end-users.
6. Technical Support:
Grease manufacturers provide technical support to help customers select the most suitable greases for their specific applications. This may involve offering guidance on proper lubrication practices, compatibility with different materials, and troubleshooting lubrication-related issues.
7. Compliance with Regulations:
Grease manufacturers need to adhere to industry standards and regulations governing the production and distribution of lubricants. This includes meeting environmental, health, and safety requirements, as well as complying with specifications set by organizations such as the American Petroleum Institute (API) and the National Lubricating Grease Institute (NLGI).
In summary, grease manufacturers play a vital role in the lubrication industry by developing, producing, and supplying high-quality greases that contribute to the efficient and reliable operation of machinery and equipment across various sectors. Their expertise in formulation, quality control, and technical support helps ensure optimal performance and longevity of lubricated components.